“Empowering Fire Alarm Engineers: The Significance of Insulation Testing in Electrical Systems”
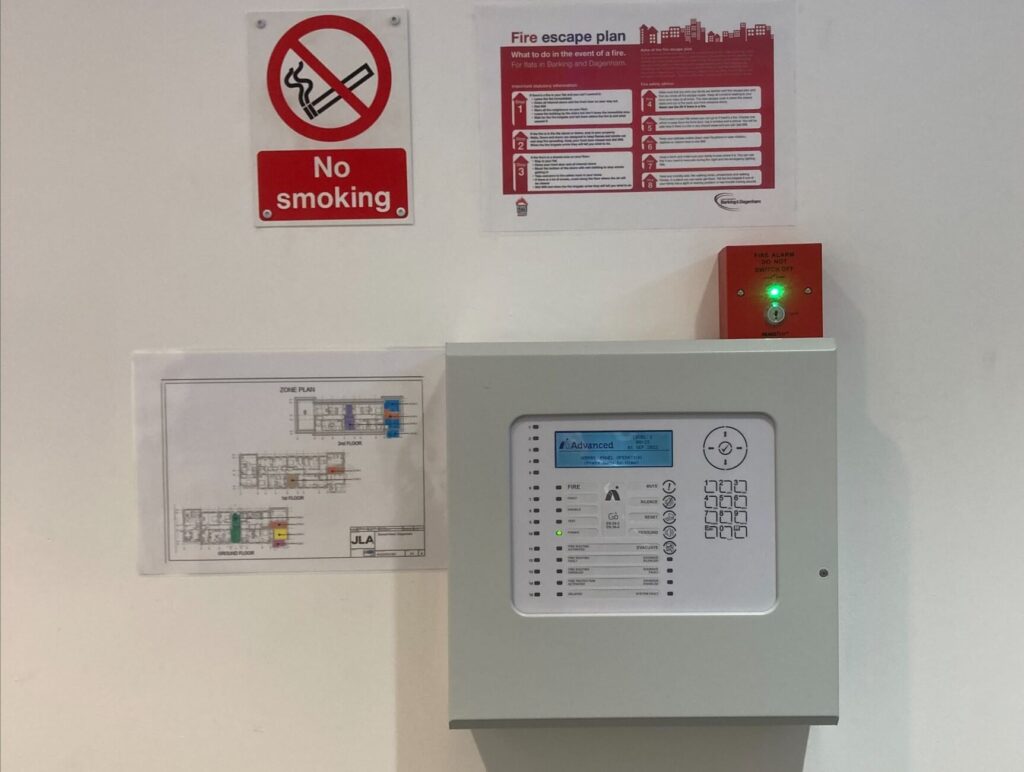
Understanding the principles of insulation testing is vital for fire alarm engineers and professionals in similar roles. Insulation testing, in the context of domestic, commercial, and industrial settings, involves assessing the electrical insulation within a given installation. This insulation typically encompasses elements like distribution boards, fixed wiring, and various accessories such as socket outlets and light switches.
The primary objective of insulation testing is twofold. First, it ensures that new electrical installations are executed correctly, upholding safety and performance standards. Second, it verifies that older installations maintain their safety standards, remaining suitable for ongoing use. Achieving these goals necessitates a combination of visual inspections and electrical tests conducted using specialised equipment. These results, in turn, are subject to verification by a competent electrician to confirm compliance with the prescribed standards.
In the United Kingdom, the benchmark for electrical insulation is set by BS7671:2018, commonly known as the 18th Edition of the Wiring Regulations, or simply the ‘Regs.’ As a part of this process, electricians responsible for the inspection and testing procedures issue certificates upon completion. These certificates serve as records of their findings and the test results, further ensuring transparency and accountability.
Over time, inspection and testing have evolved to become integral components of the electrical industry’s practices. A test meter and a collection of certificates have now become indispensable tools in an electrician’s daily routine, alongside the more traditional tools like screwdrivers, wire cutters, and SDS drills.
While inspection and testing have long been essential due to the Wiring Regulations (BS7671), their widespread adoption was significantly facilitated by the concerted efforts of trade organisations like NICEIC. Furthermore, the inclusion of electrical safety requirements in the Building Regulations (Part P) in 2005 marked a watershed moment in terms of the volume of inspection and testing carried out within domestic installations. This shift was particularly crucial in a sector that had been historically dominated by do-it-yourself enthusiasts and unscrupulous electricians.
Nevertheless, specific trades, including those involved in fire alarm systems, closed-circuit television (CCTV), and other Extra Low Voltage (ELV) applications, exhibit a slower adoption rate of comprehensive inspection and testing practices. A noteworthy observation is that fire alarm installers, as an example, often forgo insulation testing procedures, opting instead to rely on the capabilities of the fire alarm panel to identify and address potential issues.
In an era of increasing concern for safety and accountability, it is imperative that all sectors understand the importance of inspection and testing. This awareness extends to professionals beyond traditional electricians, including extra low voltage (ELV) engineers such as CCTV installers and fire alarm installers. Only through comprehensive adoption of these practices can we collectively advance safety standards and the reliability of electrical installations across the board.
“Decoding Insulation Testing: Unravelling the Basics”
Insulation testing, in the realm of electrical systems, is a fundamental process that involves assessing the integrity and effectiveness of the insulation materials surrounding conductive elements, such as wires and cables. This evaluation is essential to ensure that electrical circuits are adequately isolated from one another and from external influences, preventing unwanted electrical leakage, short circuits, and potential safety hazards. The results of insulation testing provide critical insights into the condition of electrical installations, making it a key practice in maintaining both safety and performance standards in various settings, from homes and businesses to industrial facilities.
Ensuring Safety and Functionality in Modern Electrical Insulations: The Importance of Inspection and Testing
In the electrical world, the Wiring Regulations (BS7671) stand as a fundamental pillar, emphasising two vital criteria that all electrical Insulations must meet. Firstly, they must be safe, and secondly, they must perform their intended function effectively. In simpler times, achieving these criteria was straightforward, as electrical Insulations were basic, and safety standards were rudimentary by today’s standards.
In the early days, electrical Insulation work was typically executed by local electricity boards, carried out by time-served tradesmen who worked diligently without the pressures of time and cost that modern electrical contractors face. As a result, Insulation work was generally of high quality, and the scrutiny of these Insulations was minimal.
Fast forward to the present day, and we find ourselves dealing with highly complex electrical Insulations, often installed rapidly by teams of installers, not all of whom are seasoned electricians. This transformation is accompanied by increasing demands to enhance health and safety standards and the proliferation of claims and litigation in the industry.
Even for exceptionally low voltage applications such as fire alarms, CCTV, and other similar applications, the safety and correct performance of electrical insulations cannot be taken for granted in this day and age. They ensure that electrical Insulations are not only safe but also capable of delivering their intended function reliably. They must be rigorously proven through a thorough process of inspection and testing. It is this imperative need that has given rise to the practice of inspection and testing, which forms the focus of this article.
The Power of Megger Insulation Testing
To conduct electrical Insulation testing, an electrician will typically rely on a specialised tool, such as a megger tester. The Megger MFT1741+ Multifunction Tester is a multifunction tester, which consolidates various test functions, including Earth Continuity, Insulation Resistance, Earth Fault Loop, and RCD testing, into a single instrument. These multifunction testers, often referred to as MFTs, have become the industry standard for Insulation testing. However, some electricians may still prefer to use single-function testers for specific tasks.
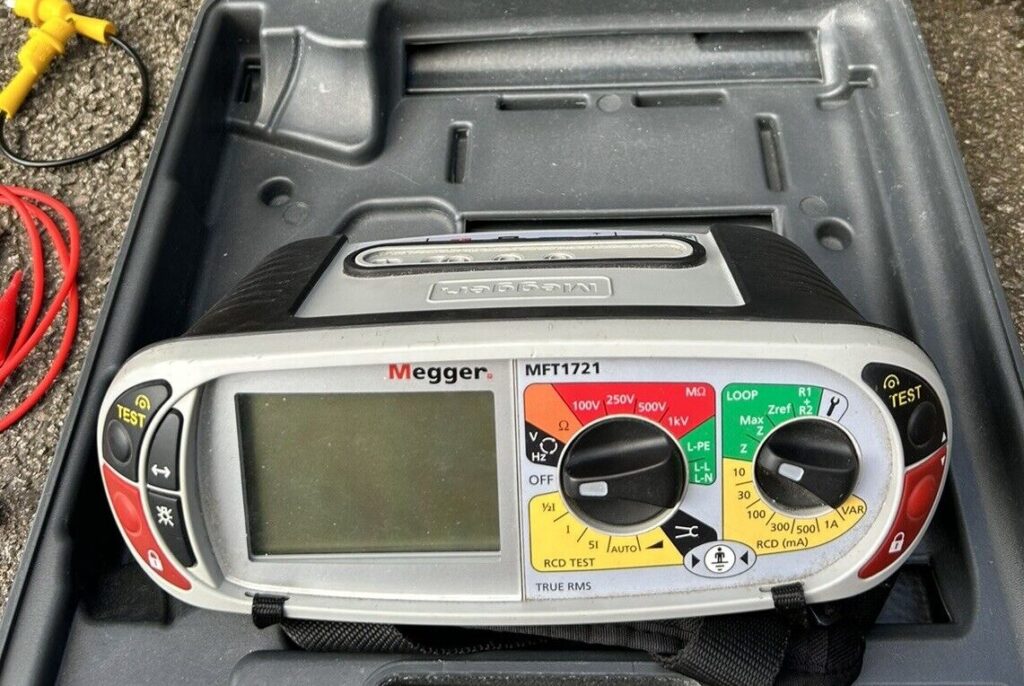
“Insulation Testing Requirements in Fire Alarm Wiring: Insights from BS 5839”
The question of whether insulation testing is necessary for fire alarm cables remains a subject of debate, particularly in light of today’s advanced intelligent Fire Alarm panels. To make an informed decision, it’s crucial to first understand the purpose and significance of the insulation test.
At its core, an insulation resistance test assesses the condition of the insulation surrounding wires and any associated equipment. Adequate insulation plays a pivotal role in ensuring fundamental safeguards against overheating, fire hazards, and the prevention of short circuits and ground-related issues.
With reference to BS 5839-1:2017 section 38.2 (a) – All installed cables with a voltage rating suitable for mains use should be subject to insulation testing at 500V d.c. Prior to this test, cables should be disconnected from all equipment that could be damaged by the test.
Certain fire professionals within the field of fire installation maintain the perspective that in the context of a 24V DC system, specifically one that is isolated from mains power sources 230V AC, the probability of core insulation contributing to an earth fault or short circuit between the conductive cores is notably minimal. This low likelihood of occurrence is generally attributed to the absence of significant voltage differentials and electrical stresses.
However, it is imperative to acknowledge that exceptions may arise under specific circumstances involving mechanical trauma, such as crushing, during the installation process. In such instances, when the physical integrity of the insulation is compromised, the risk of inadvertent electrical contact between the cores becomes pertinent.
In the event of such insulation compromise, the modern day fire alarm panels, equipped with sophisticated monitoring and diagnostic capabilities, are generally expected to efficiently detect and alert to such anomalies, ensuring the ongoing safety and reliability of the fire alarm system. These systems are engineered to provide a robust safeguarding mechanism in response to deviations from the norm.
What does the BS 7671 say about insulation testing in SELV or ELV?
Given the frequent cross-references between the fire alarm standard, BS 5839, and the electrical installation standard, BS 7671, it is pertinent to examine the latter’s provisions concerning Safety Extra-Low Voltage (SELV) systems. BS 7671 delineates the prerequisites for insulation resistance testing within Extra-Low Voltage (ELV) circuits in Section 612. This section is dedicated to addressing the safety stipulations for ELV systems and provides explicit regulations pertaining to insulation resistance testing. The subsequent discussion highlights key aspects of insulation testing in ELV circuits as elucidated by BS 7671.
- General Requirement:
BS 7671 recognises that insulation resistance testing in ELV circuits is not always practical, and it emphasises the need for such testing where it is reasonable and relevant.
- Optional Testing:
Regulation 612.3.2 states that insulation resistance testing for ELV circuits is optional and should be considered where it is necessary to demonstrate the integrity of the insulation, or if it is required by other regulations or standards.
- Selection Criteria:
Regulation 612.3.2 also specifies that when testing ELV circuits, the minimum insulation resistance values should be selected based on factors such as the type of installation and specific regulations or standards that apply to it. The selection should be reasonable and appropriate for the circumstances.
- Testing Method:
When insulation resistance testing is carried out on ELV circuits, it should be performed in accordance with the relevant standards, taking into consideration the voltage and characteristics of the ELV system.
- Documentation:
As with other electrical installations, it is essential to maintain proper documentation of the testing and results, regardless of whether the testing is mandatory or optional. This documentation helps ensure compliance and provides a record of the installation’s safety and reliability.
It’s important to note that the specifics of insulation resistance testing in ELV circuits may vary depending on the type of ELV system, the applicable regulations, and the specific installation requirements. Therefore, electricians and professionals working with ELV systems should refer to BS 7671 and any other relevant standards and regulations to ensure they are following the appropriate procedures for insulation resistance testing in their specific context.
“Navigating the Complexities of Insulation Testing in the Presence of Interconnected Smoke Detectors on the Fire Alarm Circuit”
The primary challenge lies in the potential harm to connected equipment when applying a 500V DC voltage across live and neutral points. Consequently, during insulation testing of an inactive circuit, it is common practice to disconnect items such as light bulbs and other equipment to avert damage.
How to conduct an Insulation test?
According to Regulation 612.3.2 in BS 7671, as detailed in Table 61, the minimum acceptable insulation resistance value for a distribution circuit that incorporates a distribution board or consumer unit along with all its final circuits connected is set at 1 MΩ. However, it’s important to note that insulation resistance values of this magnitude, especially in new Insulations, may necessitate further investigation.
Before conducting an insulation resistance test, it is imperative to disconnect any equipment that could potentially influence the test results or be vulnerable to damage from the test voltage. This includes devices like surge protective equipment, dimmers, electronic switches, smoke detectors, and high-frequency luminaires.
If it is not reasonably practical to disconnect such equipment, or if there is uncertainty that all such equipment has been disconnected, the following options are available.
• Insulation resistance can be measured between live conductors and protective conductors when all live (line and neutral) conductors are linked together (see to Regulations 612.3.1 and 612.3.3). There is no potential difference between the live and neutral terminals of connected equipment when this method is used.
• The applied test voltage may be reduced to 250 V d.c., but the minimum allowable insulation resistance value remains 1 M (see Regulation 612.3).
“Unlocking the Value of Insulation Testing in Fire Alarm Installations”
The most significant insight derived from this article underscores the critical role of insulation testing within the framework of a fire alarm installation project. This practice carries the potential to yield substantial time and cost savings while concurrently ensuring the structural integrity and safety of cable installations. When embarking on the process of insulation testing, it is imperative to reference the manufacturer’s guidelines and pertinent industry standards, thus facilitating an informed determination of the necessity for such testing. For further compelling articles of this nature, we encourage readers to subscribe to our newsletter. Additionally, Cube offers Ofqual-approved fire alarm and security courses, providing individuals seeking professional training and recognised qualifications with an avenue to enhance their expertise in this field. Please feel free to reach out to us for further information.
Article by:
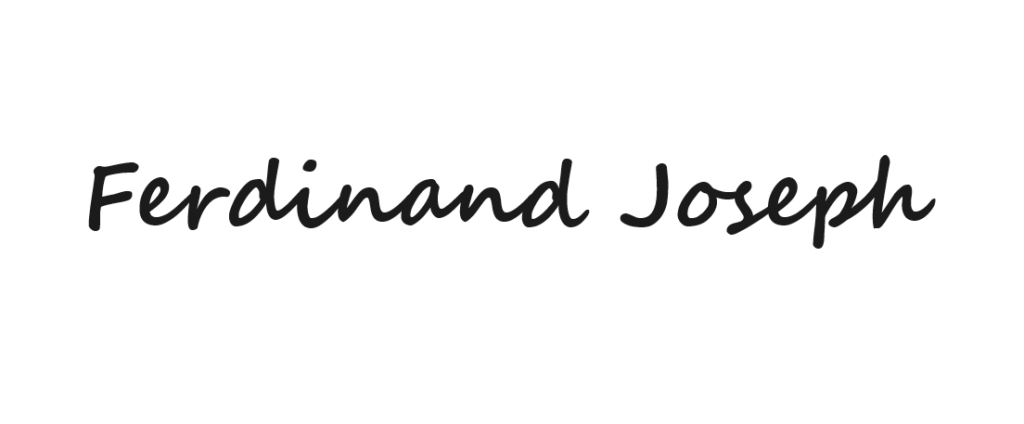
Fire and Security Alarm Consultant
“Unveil the Power of Megger: Dive into Our Next Article on Coaxial Cable Testing!” Click here